Warehousing Strategies Offer a Predictable Procurement Pipeline
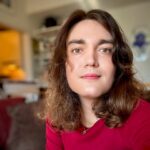
By Lyla Maisto
5 min read
Over the past several decades, advancements in supply chain management (SCM) have enabled significant cost savings and operational efficiencies in affordable housing construction. For housing providers agile enough to rapidly adapt their SCM practices, the potential dividends can be enormous, with decreased friction in the procurement of raw materials, predictable project costs and timelines, and downstream logistical efficiencies during construction itself.
As an unpredictable and volatile supply chain becomes a common reality across the U.S. construction sector, some affordable housing providers are turning to less conventional SCM strategies for advanced procurement of building materials. Expanding a firm’s advanced procurement practices through methods like large-scale warehousing of materials can help keep individual project costs more predictable amid unexpected market fluctuations.
Warehousing strategies are not common and vary greatly across the affordable housing sector. They often depend on a firm’s level of exposure to the volatility of a specific material cost center. Additionally, these strategies require a careful cost-benefit analysis, as companies must allocate significant resources to physical infrastructure, labor, and security for warehousing.
Additionally, some materials are more ‘shelf-stable’ than others; warehousing lumber, for instance, requires more advanced climate and pest controls to prevent warping or deterioration. Consequently, some firms may choose not to warehouse lumber, even as threatened increases to tariffs on Canadian lumber imports continue to unsettle both American builders and Canadian loggers.
A Worthwhile Investment
For firms that manage large construction portfolios across wide geographies, the startup costs of warehousing and the potential risks can prove worthwhile, providing a layer of insurance against unpredictable procurement issues that would otherwise inhibit or delay construction.
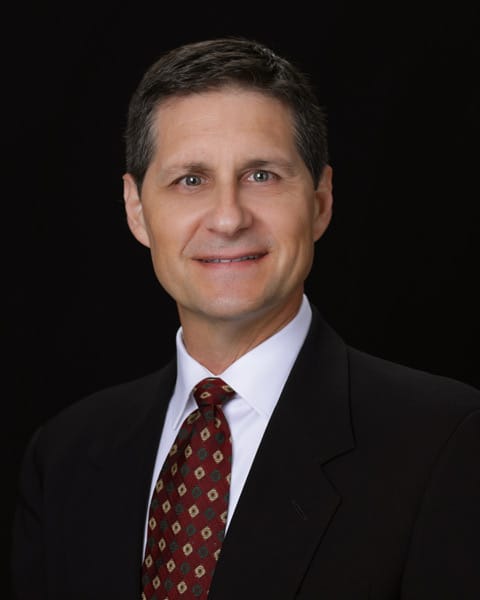
“It’s worth it,” says Tony Piscitello, president of USA Construction Management. “Even looking past a cost-benefit analysis, just for the peace of mind, it’s well worth it.”
Piscitello, whose firm handles general contracting for the large, vertically integrated, West Coast-focused USA Properties Fund, says that the practice has already proven successful in achieving its intended goal: keeping material costs predictable for the firm, as those same costs become increasingly unpredictable for others in the industry. In today’s volatile marketplace, he says, stability is a difficult thing to put a price on.
“We’re going to have the materials, we’re going to have them when we need them, and we’re going to have them at a price that doesn’t bust our budget,” he says. “
Many firms initially turned to advanced procurement during the COVID-19 era, when the pandemic exacerbated cost and capacity issues in an already-strained environment for developers. For Piscitello and many others, warehousing has become more appealing as the state of procurement continues to remain unpredictable due to the Trump administration’s waves of reciprocal tariffs, which have decreased, increased, or vanished on a whim.
“We got concerned that we could run into a shortage of supply, or unprecedented escalation of the [cost of] materials,” Piscitello says. With two new project starts, he prepared for the worst. “We have been sourcing materials outside of our normal procurement timetable,” he explains.
Strategies for Successful Warehousing
USA Construction Management has concentrated on warehousing electronic components, which might face supply shortages due to overseas tariffs on Asian electronics manufacturers. “We’re focusing on low voltage components, like electrical components, fire alarm systems, and access control systems,” Piscitello says.
Piscitello also notes the importance of including a project’s partners, emphasizing that USA Construction Management strives to account for the externalities of subcontractors who face similar supply chain issues without the benefit of their own warehouse space. For example, Piscitello says that on two projects, his team has allocated space for their framing contractors to store sheet goods, including plywood and OSB.
However, warehousing lumber, particularly dimensional lumber, is challenging due to its sensitivity to humidity, moisture, and temperature. “Especially in the summer months, we’d need to be particularly careful about twisting and spoilage of dimensional lumber,” Piscitello says. For now, he says that the firm’s framing contractors plan to utilize warehousing for sheet goods, which can have a much better shelf life when bunks (bundles) remain bound and shrink-wrapped.
For now, Piscitello is hopeful that USA Construction Management will not have to store dimensional lumber, particularly since “a fair amount of the lumber comes out of Oregon and Washington,” leaving the supply chain fairly immune from tariff uncertainty.
So, “we may or may not need that lumber storage based on the way things play out,” Piscitello says. However, “if the [lumber] tariffs hit, our speculation is that it will affect us. Whether it directly affects us or indirectly affects us, there will probably be a financial or supply chain disruption.”
Security Needs Increase
To ensure successful advance procurement, Piscitello says that USA Construction Management has had to adapt its existing “shop,” a building previously used for storing construction trailers, maintenance equipment, and a marginal stock of materials. The initiative has required a substantial investment in the security of the shop’s 5,520-square-foot warehouse, located on a 1.2-acre industrial lot in Roseville, CA.
“We increased everything on that site,” he says. “We put in new fencing with screening and razor wire along the side of the property that borders the railroad. …We just didn’t want any threats, arson, or mischief.”
In addition to the fencing, Piscitello’s team implemented solar-powered security cameras around the perimeter of the property. “If somebody comes in that’s not supposed to, especially after hours, we get notified. …We have a call list, and our general superintendent gets notified,” he says. “We’ve also paid for an additional $1 million in insurance coverage on that site.”
Such measures underscore the reality that warehousing requires investment in far more than simply physical space. As the industry continues to face losses from job site theft exceeding $1 billion per year, however, these safeguards will likely benefit the overall security of USA Construction Management’s physical plant, even when considering temporary supply chain woes.