Mountain Towns Go Modular for Faster and Cheaper-to-Build Affordable Housing
Innovative Companies Leverage Factory Construction to Avoid Pitfalls
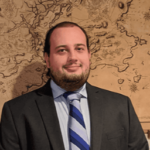
By Ethan Finlan
8 min read
Clearly, the housing crisis isn’t just confined to high-demand coastal metros. Housing supply is shrinking, and the share of cost-burdened renters is growing in the country’s interior, including the resort-oriented communities in the Mountain West. TCA reported in November 2023 that population growth has surged over the last few decades in such communities, in states like Colorado, thanks to their leisure-based economies. By extension, workforce demand has grown, but there is not enough housing at an affordable price point for service workers.
In addition to the regulatory and financial challenges hindering supply growth elsewhere in America, Mountain West states face another issue: winter weather. The severe weather significantly slows construction, worsening these regions’ supply problems. In response, Fading West has entered the market, offering modular home products that can be opened quickly.
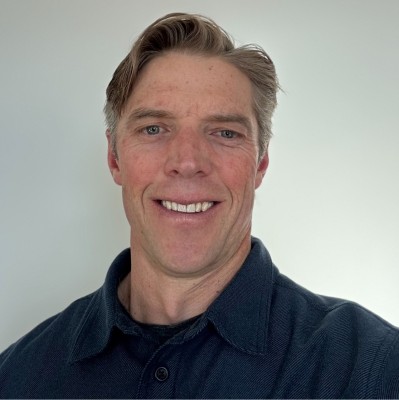
Construction slows in winter across most states, but the lengthy winters in mountain regions effectively halt construction for months. According to John Cattles, assistant county manager for sustainability and operations for Gunnison County, CO, is in Climate Zones 6 and 7 of the International Energy Efficiency Code, which imposes unique requirements for safe, habitable homes, including stronger insulation.
“It starts costing you money from November through March,” says Cattles, pointing to long durations for expenses, like soil and site treating, and particular types of glue and paint. “You really can’t start digging foundations until April, because there’s too much frost in the ground even into March. You might have a foundation ready to go by the end of June. So, you have July to the end of October to try to get your building enclosed and into a state where you can put temporary heat in.”
In addition, these towns are hemmed in by physical barriers (such as mountain ranges) or legal barriers (such as state – or federally protected land) that prevent housing development on the periphery.
Modular construction offers a clear advantage: developers can minimize weather exposure by facilitating significant indoor construction. However, the market for modular construction in these regions has remained small for several years. That changed when Fading West opened its first factory in Buena Vista, CO.
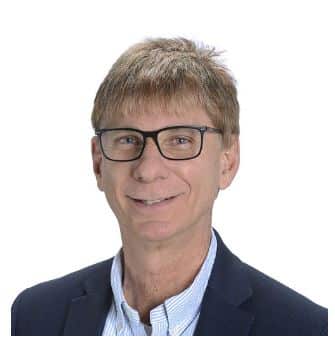
Buena Vista is a poster child for the Mountain West’s housing crisis: Rents spiked 43 percent there from 2014 to 2024, and homes became 41 percent more expensive from 2020 to 2022. The modular home market had been small for years; Eric Schaefer, Fading West’s chief business development officer, attributes this in part to the impact of the late 2000s recession and the belief that modular homes wouldn’t sell in affluent resort towns. “There has been a stigma, not only in our state but throughout the whole country, that modular means either lower quality, architecturally not interesting, and something like maybe on the lines of a double-wide trailer,” he says.
But demand grew throughout the 2010s, and high-earning professionals flocked to Buena Vista and other such locales during the COVID-driven remote work boom. This resulted in market demand focusing on high-yield single-family construction, yet the service industry workers hired to meet the needs of the expanding population couldn’t afford that.
Gunnison County faces similar issues. “We’re geographically isolated,” Cattles says. “There’s nowhere that you can reliably commute to the Gunnison area from. Our business community is struggling to keep people employed, to stay open.”
It was that demand shock that started Fading West, according to Schaefer. The firm’s first project aimed to build densely on a 22-acre parcel for residents earning 80 to 120 percent area median income. “There are very few [subcontractors], there are very few general contractors” in and around Buena Vista, says Schaefer, “so to build anything that large, over 200 homes, would have taken probably decades.” Initially sourcing materials from existing modular firms out of state, Fading West opened its factory and launched the vertically integrated model it offers today. The initial development consists of 218 units; phase one opened in 2018.
“Our whole premise was to set the factory up almost as a Toyota car factory,” says Schaefer. “We set the factory up with 18 to 20 stations. It takes about seven days to finish a house.” The factory can move structures between construction stages in a six-hour window. Schaefer describes the firm’s “dirt-to-doorbell approach,” wherein it employs in-house general contractors as key to its success. He also stresses the efficiency of working on multiple properties at a time. In contrast, other modular firms often have the capacity to only work on a single property at a given moment.
“We have in-house design plans, so that we can do two-story, or a ranch, one-, two-, or three-bedroom, anywhere from 800 to probably 2,200 square feet. We can do Accessory Dwelling Units (ADUs), and we can also do multifamily.” Schaefer states that the firm seeks partnerships with both public and private developers.
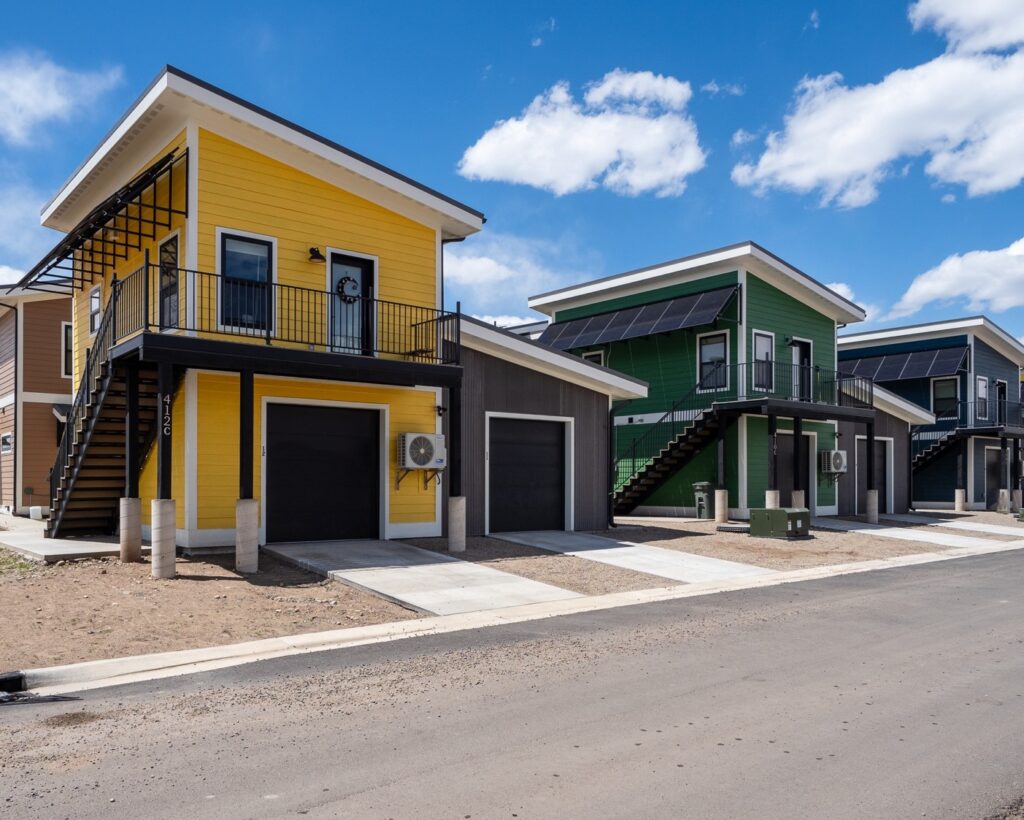
Photo Credit: Fading West Construction
The firm has a portfolio of 15 projects, including workforce housing in Vail and 54 units in Breckenridge. In Gunnison County, it undertook the Sawtooth complex, which was initiated by Gunnison County using vacant county-owned land acquired for other purposes. Gunnison County maintains ownership; Fading West acted purely as a general contractor, Cattles says, which allowed them to focus on the design and construction aspects of the project while the county handled entitlement work. According to Fading West’s website, the project serves renters earning 70 to 130 percent AMI.
“The cost was comparable to stick frame, and the timing was much faster, the schedule is much faster,” Cattles concludes. “That’s what led us to go ahead and try modular. We didn’t have a lot of hesitation, we’ve seen what Fading West has been doing in the region and [felt] comfortable they would be able to deliver, so we didn’t have a lot of concerns with using modular.”
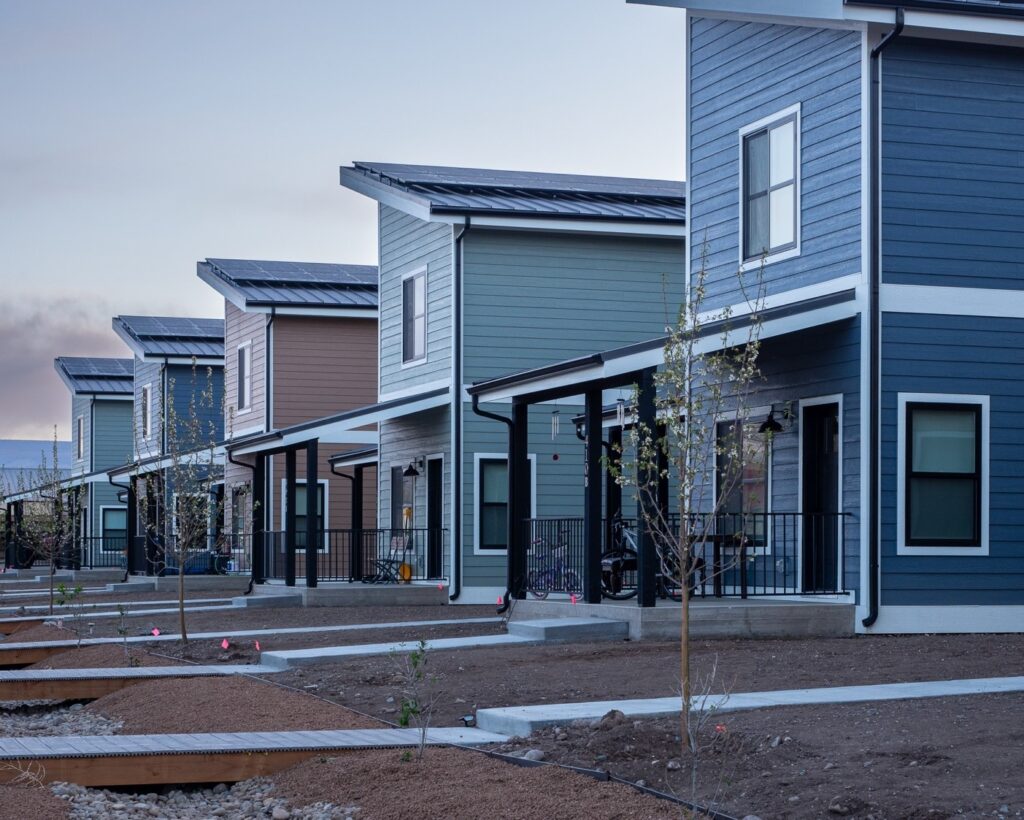
Sawtooth aims to integrate architecturally with the surrounding neighborhood while gradually increasing density in the second phase, first building accessory dwelling units on the initial townhomes, and then constructing a multifamily building further south on the lot. “Fading West was a good fit, because they could do both with the modular construction,” Cattles says.
The firm sees an opportunity not just in Colorado and other Mountain West states, but nationwide, with its high-turnaround modular methods meeting a variety of needs, including disaster relief. Schaefer notes that the firm has sold homes to individuals impacted by the Lahaina Fire in Hawaii. The firm built over 80 houses, with a two- to four-month turnaround time from construction to move-in. “These are for families that were literally living in hotels,” Schaefer points out; the homes are habitable for up to 50 years because they are International Building Code-compliant.
The firm is exploring offering homes to buyers affected by the winter wildfires in Southern California, and exploring expanded business in Hawaii, Illinois, and Wyoming. The firm envisions a partnership approach to expansion. In markets without weather constraints, Schaefer stresses that there will be less of a cost savings, but the time savings can still make Fading West an attractive option.
Schaefer emphasizes that “a steady workforce” is crucial for making the rapid factory production approach successful, and that it is vital for partners to engage with the firm early on to avoid drastic changes to the internal design; there is greater flexibility with external features. “If you went in to buy a Camry, you wouldn’t ask…to redesign a dashboard,” he says. “Work with us from the beginning…and if we can build it quicker or more efficiently, then the cost decreases dramatically. And then you can pass those savings on to the end customer.” Cattles notes that the main challenge with modular construction is that any delays result in higher costs due to reservation rates at factories.
For its part, the state of Colorado is taking several actions to promote faster, affordable housing construction. Schaefer and Cattles point to a bill aimed at creating standardized building codes for modular homes, reducing friction. Additionally, the state is offering grants and loans to manufactured housing producers. Cattles points out that more modular factories are being built throughout the state, such as Grand Junction.
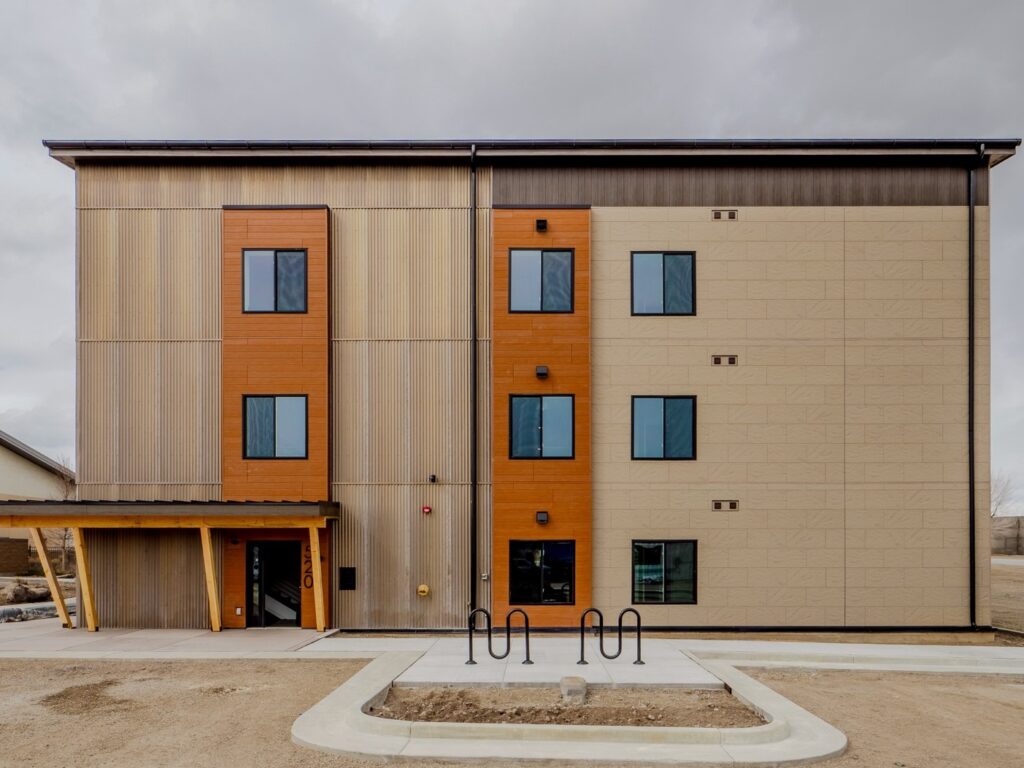
Schaefer says that Fading West is open to collaborating with a wide range of private and public developers. He believes the firm’s model is a game-changer for addressing the country’s housing crisis. “We see ourselves as a missional company. We use modular as an innovative approach to build high-quality, architecturally interesting, energy-efficient, affordable homes for both the state of Colorado and the entire country.”