Leveraging the Benefits of Adaptive Reuse
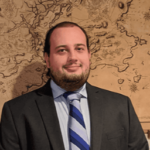
By Ethan Finlan
8 min read
Adaptive reuse can be a greener, less expensive, and more attractive alternative to new construction. For cities with a glut of older buildings, renovating and repurposing those structures can be an enticing way for politicians and planning officials to lessen a housing crisis. And beyond housing, adaptive reuse projects can increase neighborhood investment, all while providing more energy-efficient buildings and less construction-related waste.
As such, there are several financing programs to help facilitate these projects, including national and state-level Historic Tax Credits (HTCs). These have remained popular in recent years, with the Federal HTC contributing to over 20,000 new or updated housing units in Fiscal Year 24, according to the program’s annual report. In recent years, developers have been leveraging HTCs in increasingly creative ways, such as conversions of mid-century downtown office buildings into affordable housing.
Overall, the costs of adaptive reuse are lower than building a new structure, with one analysis from the Urban Land Institute estimating a 12 to 15 percent cost savings. At a time when construction costs are skyrocketing, that’s an appealing prospect.
However, it’s not as simple as converting an old mill into an apartment building in a matter of months. Adaptive reuse projects can pose unforeseen challenges, such as navigating buildings constructed initially with materials now recognized as unsuitable for human dwellings. Tax Credit Advisor spoke to two industry veterans, who say that the keys to successful adaptive reuse are to think carefully about which buildings and parcels are advantageous, plan diligently to anticipate challenges, and be aware of the best funding sources for your project.
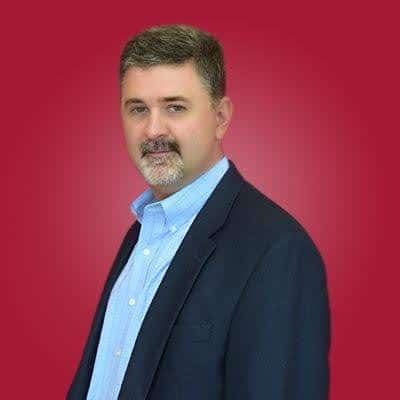
Building Selection
The first factor is whether a building can comfortably house residents. This can sometimes be challenging for adaptive reuse projects that use HTCs, as renovations may need to adhere to certain design elements required by the building’s historic designation agreement. “Oftentimes, you’d find large warehouses that are just too deep,” says John Randolph, development principal at Ingerman. “You’d be left with a very large vacant shell on the inside of the building because there are no windows and no access to light.”
Though it certainly adds an extra layer of work to a project, the rigorous review process that reused buildings go through is often a draw for investors, says Albert Rex, principal in Ryan’s Historic Tax Credits division.
Rex emphasizes that there are more HTC-eligible buildings than generally meet the eye. While some developers may assume that only very old, beautiful, and architecturally significant buildings can receive historic designation, “in reality, historic buildings have to be a minimum of 50 years old and can receive a historic designation for many different reasons, not just that they are pretty or exemplary architecture,” he says.
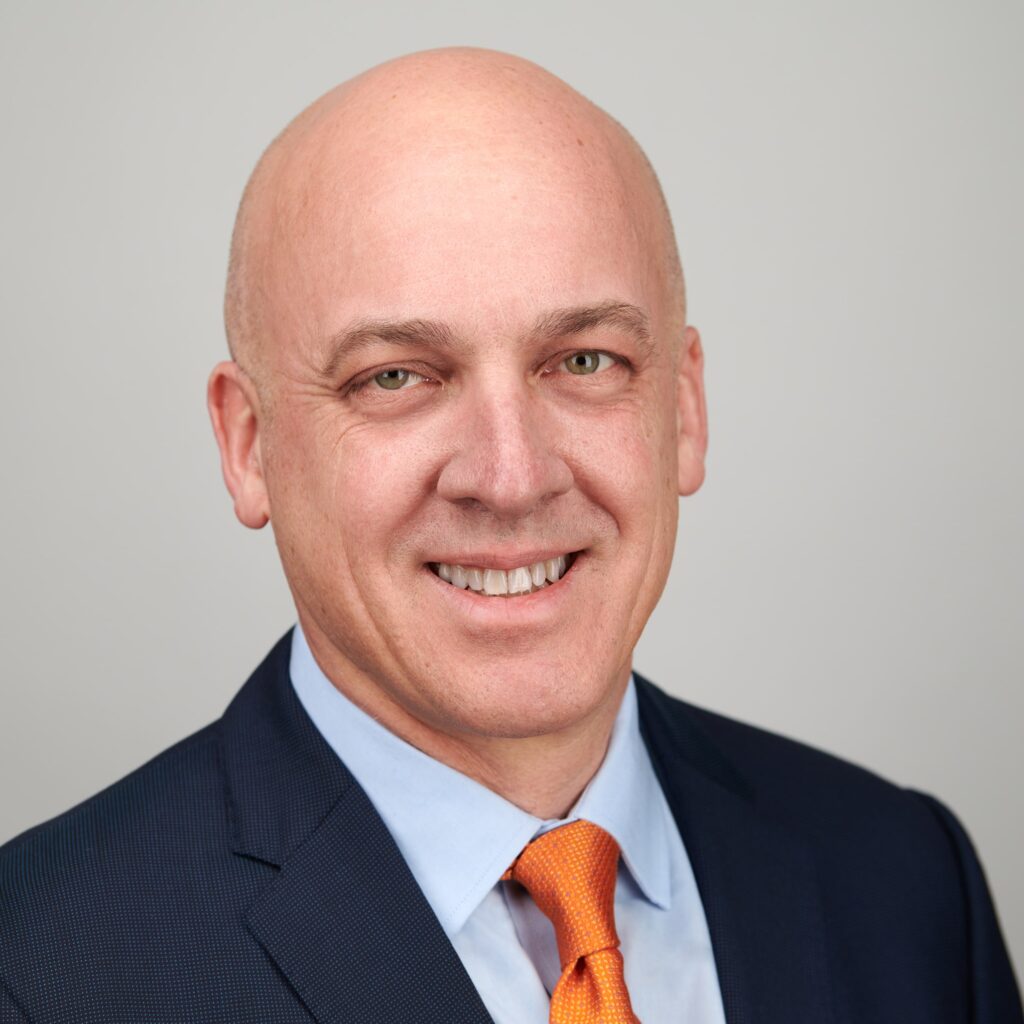
How to Plan for Reuse
Proactivity can go a long way towards reducing and managing unforeseen delays. Rex stresses the importance of including historic consultants on the project team, as well as ensuring all design changes are approved in time for credit review. Not doing so has blocked projects, albeit in “rare cases,” he says.
Randolph says that successful reuse projects anticipate rehabilitation costs. “Most buildings like this, you’re going to expect to have lead-based paint and asbestos. That’s really what you’d expect at a minimum.”
Randolph discusses a recent project his team finished in Montgomery County, PA, called the Willows at East Greenville, which required careful planning from the start. “This building was used for about 50 years by a plumbing products manufacturing company that we bought the property from. This required some cleanup that I would call atypical of a historic property, just in terms of chemicals that were still left behind.”
Additionally, the Willows required a substantial amount of historically accurate window detailing, which added approximately $500 in costs per window, says Randolph. This work was all made more difficult as no portion of the building could be demolished.
“HTC projects are just big puzzles, and like any puzzle, one of the keys to success is being patient and sometimes thinking of outside-the-box solutions to make things work,” Rex says. He says that successful reuse projects “use the historic character of the building to your advantage, not as an impediment.”
The developers on the Willows project followed that guiding principle. For instance, a boiler room was converted into a community gathering space, and water catchment infrastructure was installed under the parking lot to prevent aesthetic problems and flooding. All the while, the developers worked to ensure a faithful design in rebuilding the trusses and other interior materials.
Though the design challenges can be daunting, Rex points out that reuse projects can encounter less resistance than new build construction. “If you tell a community you are building a new 250,000 square foot building for affordable housing, there can often be pushback,” he says. “If you say you are reusing a 250,000 square foot historic building, the community can often be more supportive, whatever the use.”
Randolph’s Willows project benefited from this local support. Although the area where the building was located was originally zoned for industrial, non-residential use, the local planning commission adopted an amendment to the zoning code that allowed for the reuse of industrial facilities for residential purposes.
Funding Adaptive Reuse Projects
The Federal HTC is the most obvious source of funding for adaptive reuse projects, providing a 20 percent credit for qualifying structures. Rex says HTC usage became more common following changes imposed by the Tax Cuts and Jobs Act in the late 2010s.
The HTC application process consists of three parts. First, a building must either be listed on the National Register of Historic Places or located within a previously designated historic district. The second stage involves an evaluation of the plan against criteria established by the Department of the Interior. Faithfulness to the original design is one criterion, as is avoiding the use of materials that compromise or degrade the original elements. Rex notes that this includes taking pictures of the property and an additional review by state-level authorities. The process can be time-consuming; according to the National Park Service, state and federal review takes about two months cumulatively. Finally, there’s a second level of review once a project is done to document that the work was completed as proposed.
Additionally, 37 states have local HTCs; collectively, a project in those states “may be able to get more than 40 percent of [the] capital stack, in gross terms, from HTCs,” says Rex. States may also have specialized programs, such as Massachusetts’ Community Preservation Act, or other state programs aimed at office conversion, making projects that can layer these many funding streams particularly attractive.
The key qualities that help developers succeed in adaptive reuse, besides knowledge of building suitability, may include perseverance and resourcefulness. Having as much information about the project early on is crucial. But just as important, as the Willows experience shows, is flexibility in finding ways to turn a building’s protected features into an advantage, along with the necessary financing to complete complex projects.
Still, it is strong support for adaptive reuse projects, like the Willows, that often makes them feasible, Randolph argues. “If it were a market-rate conversion, it probably wouldn’t have yielded the rents that it needed.”
Case Study:
The Willows at East Greenville
A recent adaptive reuse renovation in eastern Pennsylvania showcases a variety of key aspects of adaptive reuse. The Willows at East Greenville is a 71-unit mixed-income development built in a partnership between developer Ingerman and Genesis Housing, an affordable housing nonprofit serving Montgomery County, PA. The project leveraged HTCs to renovate a former factory, which was used to manufacture cigars and later served as the home of Boyertown Casket Company, which made caskets for figures, including Robert F. Kennedy and Marilyn Monroe. The Boyertown Casket Company closed in the 1960s, after which the building was occupied by a plumbing products manufacturer until Ingerman acquired it in 2019.
Randolph first realized the building’s potential for housing during a tour in 2015. “This site was a tremendous historic asset,” Randolph says. “The actual physical structure itself…was in terrible shape. You look at the bones of a property, and that’s what stood out.” Still, Randolph’s team at Ingerman was able to get the structure listed on the National Register of Historic Places in 2018, the first step in qualifying for HTCs.
The design team had to address several challenges before the building could be suitable for habitation, including structural and environmental remediation, as well as various architectural systems and ceiling heights. These challenges were overcome through creative design practices and a developer willing to see the project through to its completion.
The Willows utilized a relatively diverse capital stack consisting of nine distinct funding sources, according to HUD’s post-project case study. In addition to the Federal HTC, the project received funding from Pennsylvania’s equivalent program. The project’s largest source of funding came from the Federal LIHTC program, with additional money coming from Montgomery County’s HOME funds, dollars from both county and state housing trust funds, and county redevelopment authority funds. The project also received a developer fee deferment.